Inventory refers to the stock of goods or materials that a company holds for production, sales, or resale. It represents one of the most significant assets for many businesses, particularly those involved in manufacturing, retail, and distribution. Inventory management is crucial for ensuring efficient operations, meeting customer demand, and optimizing financial performance. Let’s explore inventory in more detail:
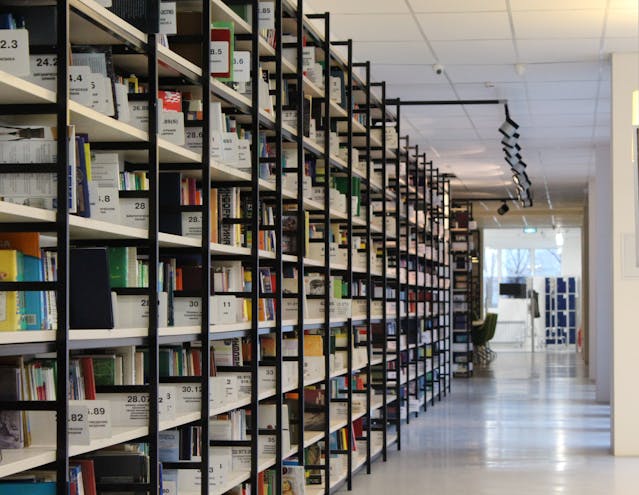
Contents
Types of Inventory
Raw Materials
These are the basic materials and components that a company uses to produce finished goods. Raw materials are in their natural state and undergo transformation during the manufacturing process.
Work-in-Progress (WIP)
WIP inventory includes partially completed goods that are in various stages of the production process. These goods are not yet finished, but have undergone some level of processing.
Finished Goods
Finished goods are completed products that are ready for sale or distribution. They represent the end result of the manufacturing or production process.
MRO (Maintenance, Repair, and Operations)
MRO inventory consists of items necessary for day-to-day operations, maintenance, and repair activities. These can include tools, spare parts, and consumables.
Buffer or Safety Stock
Buffer inventory is maintained to safeguard against uncertainties in demand, supply chain disruptions, or production delays. It acts as a safety net to prevent stockouts.
Cycle Stock
Cycle stock is the regular inventory a company maintains to meet its expected demand during a specific time period. It represents the portion of inventory that is continually replenished and consumed.
Importance of Effective Inventory Management
Customer Satisfaction:
Maintaining optimal inventory levels ensures that products are available when customers demand them, enhancing customer satisfaction and loyalty.
Working Capital Optimization:
Efficient inventory management prevents overstocking and stockouts, optimizing working capital by minimizing tied-up funds and avoiding costly stockouts.
Cost Control:
Effective inventory management reduces holding costs, including storage, insurance, and depreciation expenses. It also minimizes the risk of obsolete or perishable inventory.
Supply Chain Efficiency:
Well-managed inventory supports a smooth and efficient supply chain, enabling the timely production and delivery while minimizing disruptions.
Profitability:
Balancing inventory levels with demand helps maximize profitability by minimizing unnecessary costs, preventing lost sales opportunities, and avoiding discounting excess inventory.
Financial Reporting Accuracy:
Proper inventory management ensures accurate financial reporting, preventing distortions in financial statements and facilitating more informed decision-making.
Strategic Decision-Making:
Timely and accurate inventory information empowers businesses to make strategic decisions regarding production planning, pricing strategies, and market positioning.
Inventory Management
Forecasting and Demand Planning:
Analyzing historical data and market trends to forecast future demand and determine optimal inventory levels.
Inventory Control:
Implementing systems and procedures to monitor inventory levels, track movements, and prevent stockouts or overstocking.
ABC Analysis:
Segmenting inventory items based on their value and significance, prioritizing resources and attention accordingly.
Just-in-Time (JIT) Inventory:
Minimizing inventory holding costs by replenishing stock only when needed, reducing excess inventory and waste.
Inventory Valuation Methods
FIFO (First-In, First-Out):
Assumes that the oldest inventory items are sold or used first, reflecting the cost of goods sold based on the earliest purchases.
LIFO (Last-In, First-Out):
Assumes that the newest inventory items are sold or used first, reflecting the cost of goods sold based on the latest purchases.
Weighted Average Cost:
Calculates the cost of goods sold and ending inventory by averaging the costs of all units available for sale during the accounting period.
Challenges of Inventory Management
Excess Inventory:
Can tie up working capital, increase storage costs, and lead to obsolescence or spoilage.Stockouts:
Result in lost sales, decreased customer satisfaction, and potential damage to the company’s reputation.Inventory Shrinkage:
Occurs due to theft, damage, errors, or mismanagement, leading to financial losses and inaccuracies in financial reporting.Example
Imagine a retail store preparing for the holiday season. By stocking up on popular merchandise well in advance, the store ensures it can meet increased customer demand during the busy shopping period. Effective inventory management systems track sales trends, monitor stock levels, and replenish inventory as needed to optimize sales and maximize profitability.
Summary
Inventory plays a pivotal role in the operations and financial performance of businesses across various industries. Efficient inventory management practices are essential for maintaining competitive advantage, meeting customer expectations, and driving sustainable growth.
8 thoughts on “Inventory 101: A Comprehensive Guide to Business Assets”